Case Studies
These are just a few of the hundreds of custom products, parts, machines, and solutions we’ve created for our customers over the years.
If you’d like to hear more about these cases, or a case closer to your own needs, just give us a call and we’d be happy to share those successes with you.
A mid-sized meat processing plant was running a sausage linker that was able to produce 800 sausages per minute. When their demand increased and they needed to increase production, they found their linker could not keep up with the higher demand and it was experiencing constant malfunctions. And this caused downtime and delays they could not afford.
They came to us for a solution and we designed an entirely new machine for them. This new machine is capable of producing 1400 sausage links per minute, a 47% increase in production. In addition, the new linker we designed requires very little maintenance, allowing them to keep it running longer. Their facility now processes more than 100,000 pounds of pork every day with our machine.
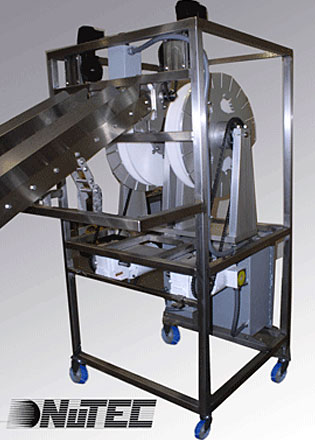
Pig Wash
Before pigs are processed into food, they are completely washed. The typical pig wash looks very similar to a car wash, the kind with Christmas tree whips. The whips are plastic and organized along two 12-foot-long shafts.
A client came to us and told us the steel shaft on their pig wash would rust over time and wear out. This happened before, but this time the shaft wore out at a critical time for the organization as one of their other facilities closed and now they had to double their production volume.
We were able to redesign the shafts without having to remove them from production. And we also determined that using stainless steel would prevent the machine from having these issues in the future. We went into the facility overnight and installed the new shafts during their maintenance period, and they have not needed replacement since.
Bottle Production
We were approached by a bottling company that was having issues with product falling from upper level conveyors onto ground level production units. This would break the lower level machines and cause a complete line shutdown until it could be repaired.
We traveled to the facility, diagnosed the problem, and took a series of measurements so we could design a solution. What we came up with was a safer and more resilient machine guard. We installed the improved product overnight and it has allowed the facility to avoid shutdowns due to falling product ever since.